Turbine Technologies, LTD has just finished installation, training and initial operation of a new computer-controlled, two-axis abrasivejet system for use in its aerospace engine development projects and for general machining in support of the educational products division. A machine manufactured by OMAX Corporation of Kent, Washington was selected and should provide the necessary capacity for the forseable future.
Abrasivejet cutting is an advanced form of waterjet cutting. Water is pressurized to 55,000 psi and forced through a sapphire nozzle at 2,500 fps. Garnet abrasive is injected into this water stream, mixed in a ceramic mixing tube and discharged at 1,000 fps. This high-speed jet of water and abrassive is then directed at the material to be machined. The abrasivejet's cutting action is a grinding process using the forces and motion of the water rather than a solid grinding wheel.
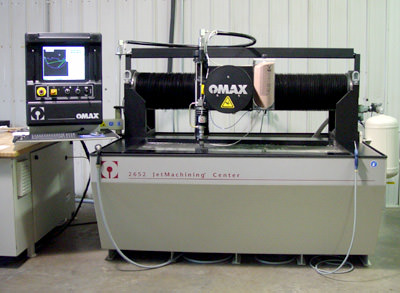
The abrasivejet process is ideally suited for extremely hard materials like those found in the Company's gas turbine engine products. Inconel sheet utilized in the engine combustion can is particularly difficult to cut or drill. The computer-controlled capabilities of the OMAX machine allows new combustion can designs to be downloaded directly and produced within minutes. This capability integrates well with the Company's other CNC machines and rapid prototyping tools. It greatly facilitates the design-production-testing cycle Turbine Technologies, LTD is known for.
The machine works equally well with a variety of other hard material like glass and soft materials such as plastics and composites. There are essentially no materials that cannot be cut with the abrasivejet machine. Material thickness can range from thin sheet to solid blocks of 18" and more. Parts can be finish machined directly with the OMAX abrasivejet with tolerances better than 0.003".